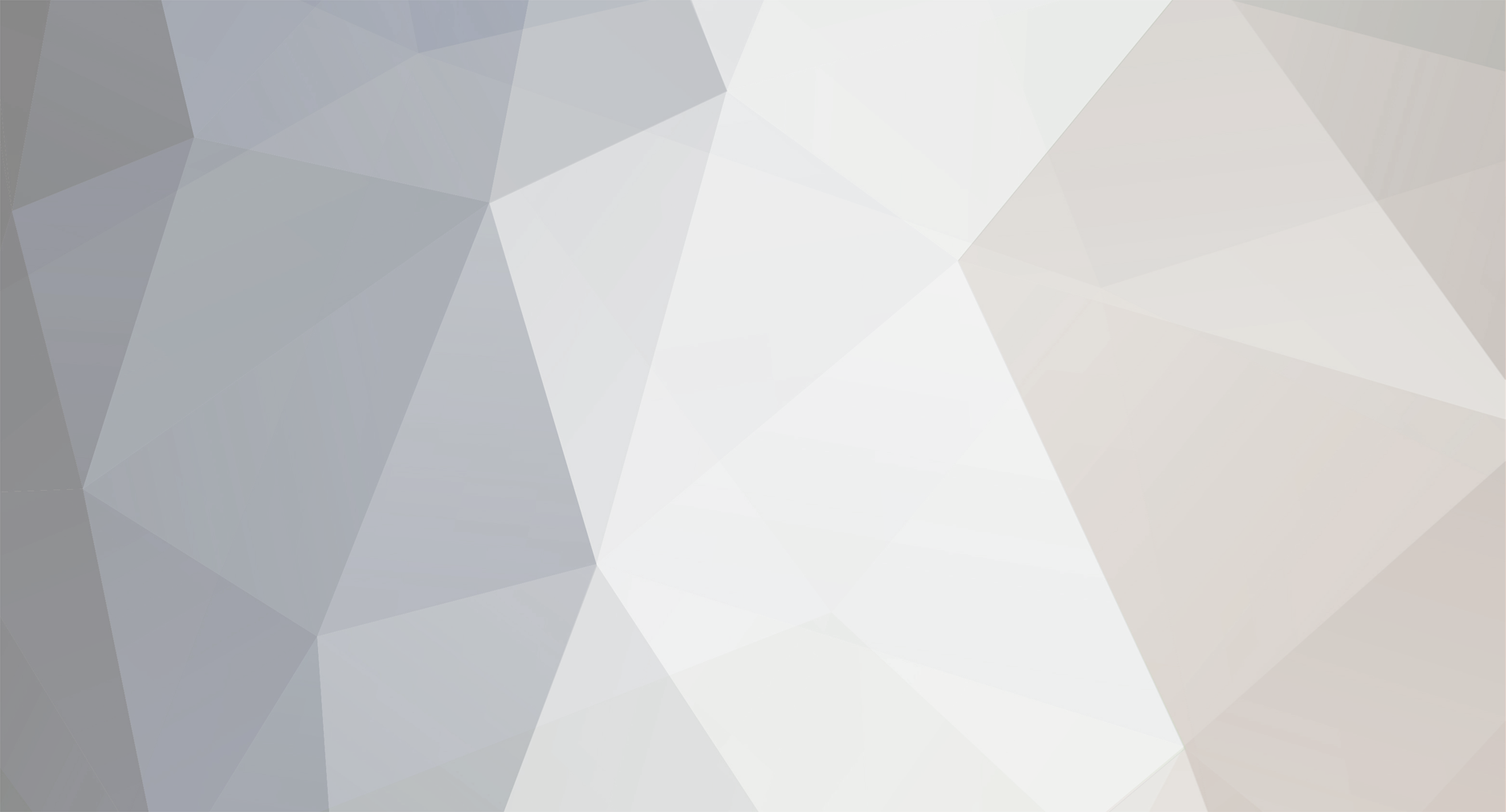
Borjawil
Journey Member-
Posts
78 -
Joined
-
Last visited
-
Days Won
3
Content Type
Profiles
Forums
Gallery
Everything posted by Borjawil
-
Well misfire in cyl 1 solved. Dtc came back when I drove the car from driveway to street to move it. Spark plug Tang was smashed into the electrode some how. No idea. Replaced, started a few times, revved engine, rechecked and new one isn't smashed. No idea. Still have o2 sensor code. Need to swap the sensors yet, but I also have a leak where the cross under pipe meets the rest of the exhaust, so going to fix that first and see if it resolves it.
-
Also won't rev past 3k Same o2 sensors as before but not sure if there was a dtc for it. I'll double check injector with screwdriver. Coolant leak not fixed. The two o-rings about a half dollar size between timing housing and block was leaking. Trying to find replacements but can't seem to find the correct part number. Any help on those two and the bigger one for the water pump? Not the squiggly one, the bigger circle one also between housing and block.
-
If they are correct p0038 identifies high voltage on that bank 1 sensor 2 circuit. Ideas if sensor is ok? I may swap the 2nd sensors around and see where that gets me.
-
No problem, figure it'll help someone diag their own issues. Swapped coil from other engine and no longer a misfire code or inconsistent rattle. I do have a tapping noise that is consistent. Maybe valve noise? Not sure. Only code is p0038 for bank 1 sensor 2 o2 sensor. Swapped with used, same code. Manual is iffy on o2 sensor locations/connectors on harness side. To confirm swapped bank 2 or front most side of engine sensor connectors and got a code for bank 2. Makes sense. Swapped rear most (firewall side) and either get p0038 or p0032. I have my higher or bank 1 sensor 1 connected to connector on passenger side or front of engine, and sensor 2 to the trans or back of engine side. They reach each connector about the same. So that's no help. If anyone can confirm correct side that'd be great.
-
Had a p0300 for random misfires, and now several restarts and just a misfire in cylinder 1. Swapped injector out same thing. If I remove either coil or injector plug there's no change. I get a code set for coil plug, not code set for injector plug, when removed. Going to go ahead and swap the coil out, then spark plug if the issue hasn't changed.
-
Going to test by pulling plug to plug coil then to injector and see if there's any difference. Will update shortly.
-
09 3.5 fwd 115k - engine swap, new platinum plugs- they don't have the normal curved Tang for connecting to point of plug, but a split type end on the Tang. Just thought I'd throw that out there in case the plugs aren't correct. making progress on this car from hell. Had put together. Engine ran but had to give it gas or it'd die. Missing badly due to crank sensor not reading flywheel well. C12xx code for crank sensor and p0660? I think for crank sensor as well. Took back apart hammered the flywheel (bent in a spot), and back together now. No more crank code. One o2 sensor not connected cause one wire got pulled out. So dtc for sensor and one for air sensor on the airbox as it's not put back on yet. No other dtcs. Starts right up, runs rough, and there's a tapping from rear of the engine. It's not consistent. Almost like there's a dead cylinder/misfire or bolt bouncing around in the valve cover. Comes and goes but not consistent with idle or gas pedal/rpms. There is a fuel injector connector on that side that the clip broke. It's pushed on but you can pull it off without pushing the tab. Maybe bad connection? Just looking for ideas. How do I check for consistent power to plug coil (over head coil with 2 wires) and consistent connection to fuel injector? Other ideas on what it could be? Appreciate the help. Almost there.
-
09 3.5L 114k just swapped in a used engine. Noticed a coolant leak coming off the oil pan behind ac compressor. Removed compressor and see the plastic housing that connected the small and large coolant lines. Thought it was the gasket or housing. Cleaned up surface and replaced housing. Still leaking. I can see it coming from above that at the corner of the front head gasket. its running down/off the corner of the head gasket that sticks out past the mating surfaces. Ideas? Id say coolant pump under timing cover, but that sits in the middle of the engine and lower if im not mistaken. Note that this is occuring just by filling the collant reservoir. engine not running.
-
Well swapped flywheels out. Can't get things to line up up correctly. Not sure if anyone knows but the extra "ridge" on the fly wheel with the square cut outs is for a sensor to read. Does that go over the torque converter or just touches it? It looks to be about 1.5" wide, where as the torque converter raised bolt holes are only about .5" The trans is basically loose in the engine any resting in the cross member, as you have to undo all mounts. At this point I'm going to lift the engine out of the vehicle and see how the other flex plate fits on the converter. Then I'll likely remove the trans and mate it to the block, then see if I can get them in through the top. There looks to be enough room if you go at an angle with the trans pointed downward.
-
To add to the above for transfluid. 3.5l 6 speed trans take 4qts of fluid unless it's a new or completely dry trans. Theres no dipstick unfortunately. But I have another question if anyone knows. Looking at the torque converter and flywheel or flex plate there are four raised points on converter. Usually ive seen flex plates and converters only matching up one way, but looks like it could go together at any 90degree point for the bolts holes. However, mine is binding with the block and trans bolted together. Can't turn the flywheel. If I loosen bolts so there's a 1/4-1/2" gap I can turn. But hard to tell if converter is doing free like I believe it should. I've roasted fly wheel 90 and 180 and 270 degrees from where I started and same thing. Before I pull apart any advice or anyone know if it mates a specific way? I know the fly wheel bolts get tightened after the block and trans are bolts. Manual says to tightened the bottom two bolts on engine first then do the converter bolts. Still binding.
-
He sent me a pm. But I figured it out. In my other post on how to pull engine.
-
Adding to this. You can fill trans from top. Plus says for dealer use only. Its under the airbox
-
Figured it out and pulled from the top. Actually on of the easiest pulls ive done. Ill try to do a write up and video for youtbue as well. But for now the main points are 1) dont disconnect AC or power steering pump and lines. leave it hanging. 2) I removed both axles but Ive seen that only the driver side needs to be removed. Slides right out, pass side the support needs to be removed and then itll come out. 3) catch all the trans fluid when pulling axles and separating from engine. Apparently there is no fill plug, but I havent confirmed this yet. Major design flaw if so. 4) rear trans and top trans mount need to be removed. Easiest done by unbolting top one from vehicle, dropping the cross bar under the trans, and then access to the 3 bolts facing the wheel well can be gotten to. Oh and remove the top engine mount. Either use a jack or your engine hoist to support everything. Once the mount is removed from the trans and vehicle, raise it back up, bolt the cross member, and pull the engine. Use a leveler so the engine slips away from the trans. Dont forget to remove your flywheel to torque converter bolts. 4 of them, theres an access panel underneath. 5) youll need to remove the crank dampener, alternator can stay on, belt tensioner can stay as well. 6) make sure to drain coolant from radiator, big hose on pass side underneath, and the smaller hose on the front lower that connects to the plastic barb that clips on to the block (weird plastic square block thing) 7) rear manifold can stay on but easier if its removed. I pulled with it off, and installed with it on. wasnt a huge hassel, but the cat and o2 sensors tend to catch on the heater core hoses. Easily remove manifold with engine in. Not sure why a lot of people make a stink about on bolting it. Remove the heat shield and climb on top of your engine bay. Knees on header panel above radiator and bend over. 8) remove wipers to remove plastic on firewall to windshield. Theres a plastic box under that. Youll want to remove plastic box if you remove or install with manifold on. super easy to remove. 9) I did not remove the radiator, fan, front clip, fenders, etc. that ive seen the 2 or 3 videos do on youtube. Unecessary. 10) there are bolts from the engine to trans and trans to engine. 4 18mm on trans to engine, and 6 or 7 from engine side to trans. Starter needs to be removed. thats really about it. besides the upper intake and wiring harness, airbox, etc.
-
Casey, shot you a pm to see how you pulled it from the top and how you did so while.leaving the trans in. Trying to drop my engine through the bottom and leave the trans but whatever works.
-
Swapping a 3.5 in an 09 journey fwd. Got everything unbolted to remove engine. Using a wooden dolly to hold engine. Saw a couple YouTube videos that don't explain it too well. Basically they say to remove the trans mounts. But what holds the trans then? Another jack? I've started lifting the vehicle and the trans and engine have separated approx 1/2-1". But the engine can't slide to the pass side any further as the block where the top mount goes hits the frame/wheel well area.
-
Got the pulleys replaced, but either the rear head is warped or their is valve damage I'm guessing. Only recorded the above dtc and 0300 for random misfires. Not very helpful. But at this point I'm going to swap in the other engine. Spent too much time on this one and I'd rather not waste more time swapping the head to find another issue. I'll investigate further once I have it out of the vehicle and can more easily test things.
-
Ok so, both pulleys replaced, set timing, it fired and died. Then will only start if I give it gas at wide open the feather it around half throttle to maintain 2-3k. However it sounds like a rattle, like its only running on 3 cylinders. looking further into things. I cannot be 180 degrees off as long as pulleys are on the right cam, and cams are in the right head, and all marks line up correctly. Its full proof. heres what I did notice when I was checking I was at TDC of the compression stroke (EX and IN valves should be closed), the exhaust rocker for #1 wont move. Theres just a slight amount of pressure on it. If I put a wrench on the cam bolt and pull towards be or CW, just to put some pressure on it, then I can move the EX rocker. So after doing this, I rotated the CCW and noticed my timing was off, until I rotated CW again. Which got me thinking, could there be an extra tooth or two between my pulleys causing my issue? Also have a P2172 code for sudden high air flow detected. Not sure if thats from me flooring the gas pedal.
-
Leak down test showed 20% leakage at all cylinder except the pass side front cylinder at about 10%. Front middle cylinder definitely air come from lower intake manifold. all others I can hear a leak but cant find the leak. Not coming from exhaust, coolant reservoir (no bubbles), dip stick tube or oil cap opening. Test was done with pass side rear cylinder at TDC. Not sure if each cylinder should be at TDC when doing that particular cylinder. Please confirm. If I up the PSI through leak tester, I can hear air coming from other two rear plug holes (all plugs removed. Tells me head or gasket to blame. Rechecked compression. front 3 pass to driver side at 115, 125, 115. Rear head still at 0 on all 3. Exhaust manifold still connected.
-
if you google 09 journey cam pulley youll see. The knub or key is part of the entire pulley as far as I an tell or very seamless. As for the compression test Im assuming you mean the rear exhaust manifold? I have not detached this when checking. I feel as if manifold on would help bump compression and not keep it from showing. Correct me if im wrong and feel free to explain. My TDI jetta has locking wedges (SOHC) however it doesnt show them to be used in the manual for the procedure on this engine. But Since everything lines up I dont see it being needed. . Just got the timing cover off and everything is lined up correctly. Going to remove the pulleys again to confirm keys. Going to replace the rear head if theyre good. Only thing at this point I can see being the issue. If I were to do a wet compression test and I show compression, Im assuming it would lead to rings/pistons being the issue correct? Cant see a wet test affecting valves. I could do a leak down test to confirm valves as well. Oh one more thing, passenger side rear cylinder is #1? Want to make sure Im not checking the incorrect cylinder for TDC.
-
John, the pulleys are cast as far as I can tell. The key is a part of it. I just took the pulley off the other engine I have. Same F****ing issue. No compression in the rear 3 cylinders. I feel like im going insane. Im REALLY good at replacing the timing belt though so theres that. A few questions because im starting to doubt my own sanity. 1) Some engines say to remove all or just the plug for the cylinder youre testing compression on. I dont seem to get different readings so far, but wanted to confirm the correct procedure 1a) when testing the rear cylinder compression, and this may seem like a silly question, but removing the top intake manifold is the correct way yes? 2) when setting the timing, 1) loosen tensioner (i loosen the two 13mm bolts to the assembly) 2) loosen rocker bolts - i find if my rocker bolts are tight I can not set the timing as the cam will rotate CW or CCW when setting it on the timing mark. As if the cam lobes or sitting on the point of the lobe (but that was also before I knew the pulley key was sheared) 3) turn crank clockwise till mark lines up (little point on back of gear to point "TDC" mark on block 4) put belt on crankshaft gear, then around the front cam pulley ( I set it 1 tooth behind as when the tensioner is tightened itll jump forward), then around the rear cam pulley (also one tooth behind), 3) tighten tensioner and check timing 5) rotate crank two revolutions to same TDC mark and block and check cam alignment. 6) tighten rocker bolts 7) I like to remove the fuel pump fuse and turn the engine over and recheck timing to be sure. Is it something Im doing incorrectly here? and 3 question - The only way I can see there being absolutely no compression in a cylinder let alone 3, would be severely damaged block/cylinder, piston, head, incorrect installment or broken compression gauge, or cam not timed correctly thus opening closing valves incorrectly. I know its not the gauge or use of it. I fixed the pulley but will again tear into it and check. I cant see the back side of the block, but am ruling this and piston damage out as it ran before. Id say the head is fine too as it ran before but may be warped (though Id expect some compression still). So that leaves cam/timing issues thus the above procedure Ive used. 3a) another thought, and again seems silly, but would the front cam pulley key (I didnt check cause im an idiot) slipping as the rear did cause the rear cam timing to be off? When I check compression in rear (intake off fuel disabled or not, spark still going) I get literal fire out of the lower intake manifold. So im getting explosions. Im assuming from front 3 cylinders but Hard to tell.
-
Looks like the key on the pulley sheared off Just enough to not rotate the cam well enough but by hand would turn and stay in place when setting the timing. Looks like its part of the pulley? im guessing filling the gap and using a removable key would out of the question?
-
Wont start after head gasket replacement
Borjawil replied to Borjawil's topic in Engine & Transmission
Looks like the key on the pulley sheared off Just enough to not rotate the cam well enough but by hand would turn and stay in place when setting the timing. -
I'll give the wet test a try. Hard to believe all three ring sets are broken to the point of not compression though. I'll double check the pulley as well. See if I can have someone crank it while i watch/use a paint marker. Recovering from the surgery well so hoping I can get it done today.
-
09 3.5l blown head gasket. Fixed head gaskets. No compression on left or firewall side cylinders. Needle doesn't even move. Even with a bad valve, rings, etc. I'd have something if I'm not mistaken. Only thing I can think of is a cam, timing, or rocker issue. First time around no compression so I checked timing. Timing was about a tooth or 2. Reset timing, tightened timing belt tensioner, turned engine over at the crank and it was still spot on. Tightened rocker bolts and put everything back together. Same issue. Figured the head gaskets weren't on the correct side or timing jumped. Checked timing again to be sure. Aligned. So I checked head gaskets. Incorrect sides per alldata site. Corrected. Set timing again. Double checked it. Everything back together. No compression. Either the rear cam pulley is slipping due to a slightly sheared key that catches with slow hand turned revolution but not starter torque...or idk. So I'm here for any help I can get.
-
Wont start after head gasket replacement
Borjawil replied to Borjawil's topic in Engine & Transmission
Just saw your above post on the aluminum block stuff. Not my first rodeo in head gaskets or rebuilding engines. Car ran before tear down just fine, no noise, just coolant mixing with oil. Started right up and drove even. True the head could have warped, but I've never seen no compression on an entire side after it was just running. As far as the head not being able to be removed with engine in, that's what the manual says. I've been through plenty of procedures that require an obscene amount of time to do naccording the service manual...like 8 hours but actually only take an hour if you're a bit slow. The service manual says it can't be done because you can't remove the cams with the heads in, the cam bolts are super long, etc. I've done it twice now so pretty sure ya can. Just need to finaggle it. But at this point I'm going check the compression on the other engine before swapping it, and then figure out what the hell is going on with this one when I get it out.